Vernon Pump Station for Ellington Sewerage Entering Vernon Wastewater Treatment Plant
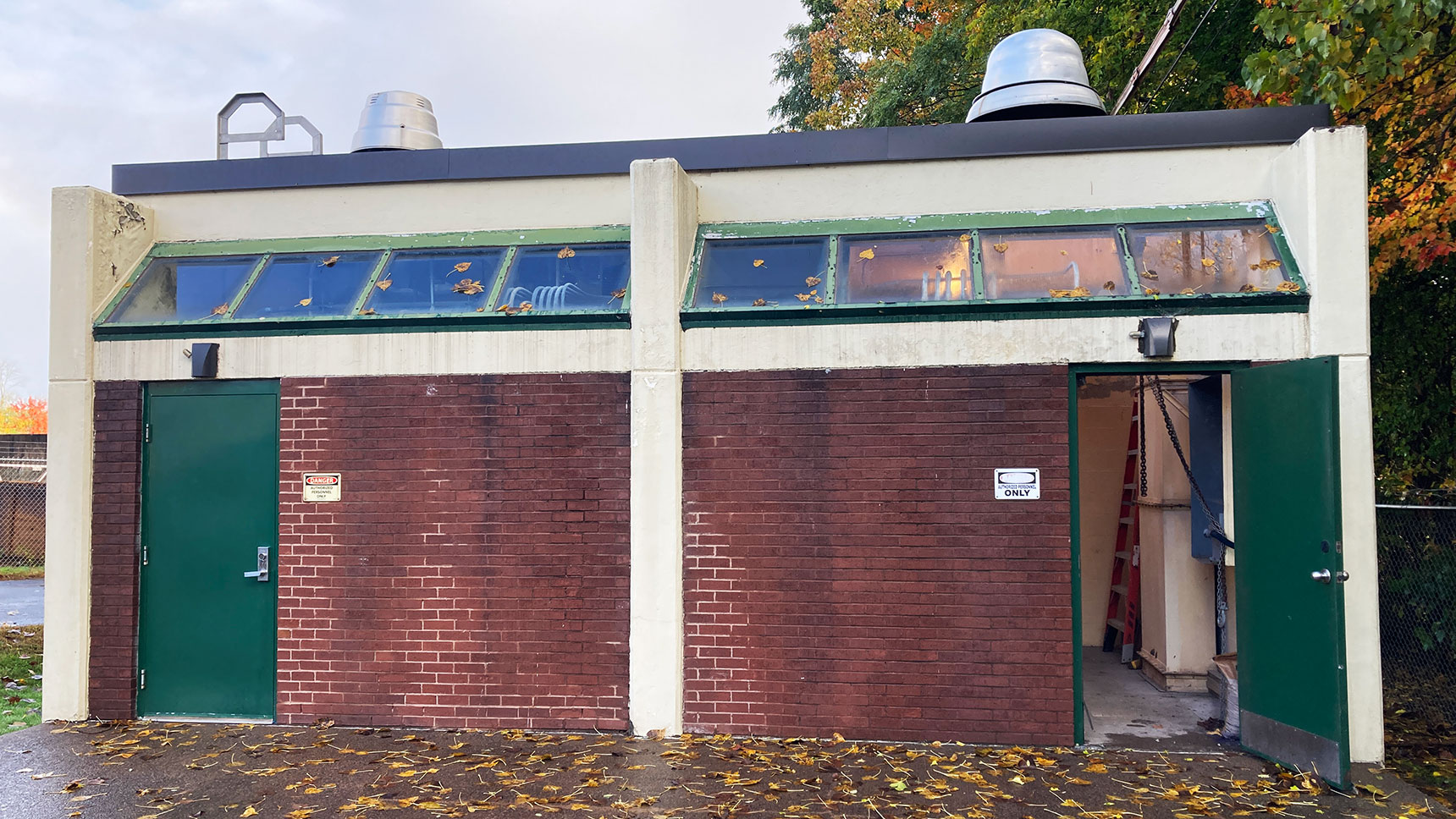
The Vernon Pump Station was facing challenges including aging control technologies, operational hardships, and increased wastewater flows as a result of proposed developments and a sewer extension within the sewershed.
The Ellington Water Pollution Control Authority (WPCA) hired Fuss & O’Neill to evaluate the Vernon Pump Station for capacity and operational improvements.
Our evaluation and Preliminary Design Report determined that the existing pumps were inadequate to pump both the existing and proposed (from future proposed development) wastewater flows. To upgrade the pump station, three new 25 HP horsepower (HP) pumps and VFDs would be required to replace the three existing pumps. As a result of the new, larger pumps, the existing 80 kW generator also needs to be replaced. Its proposed replacement is a pad-mounted 250 kW generator be placed outside.
The Report also identified the need to upgrade the internal piping, valves, pumps, electrical wiring, lighting, ventilation, controls systems, and other ancillary equipment. The Report recommended replacement of deficient or undersized equipment to improve reliability, to take advantage of new technology, and to standardize pumps and other components.
Previously identified safety improvements, as noted in the Report, will be included as part of the overall work. The deliverables will be composed of contract documents (technical specifications and plans) for bidding of the recommended improvements and a definitive level opinion of project cost to upgrade the pump station.
In an effort to reduce lead times and save some capital cost, Fuss & O’Neill’s wastewater engineers worked with Ellington staff to complete technical specifications so that the Town could pre-purchase the new Flygt pumps, the new larger backup generator, and a new sluice gate for the pump station in advance of project bidding. This helped to expedite the construction schedule and included specific language for the contractor to install the pre-purchased equipment and work with the vendors for the testing, startup, and placement of the equipment.