Design-Build Projects: A Collaborative and Refreshing Approach to Construction
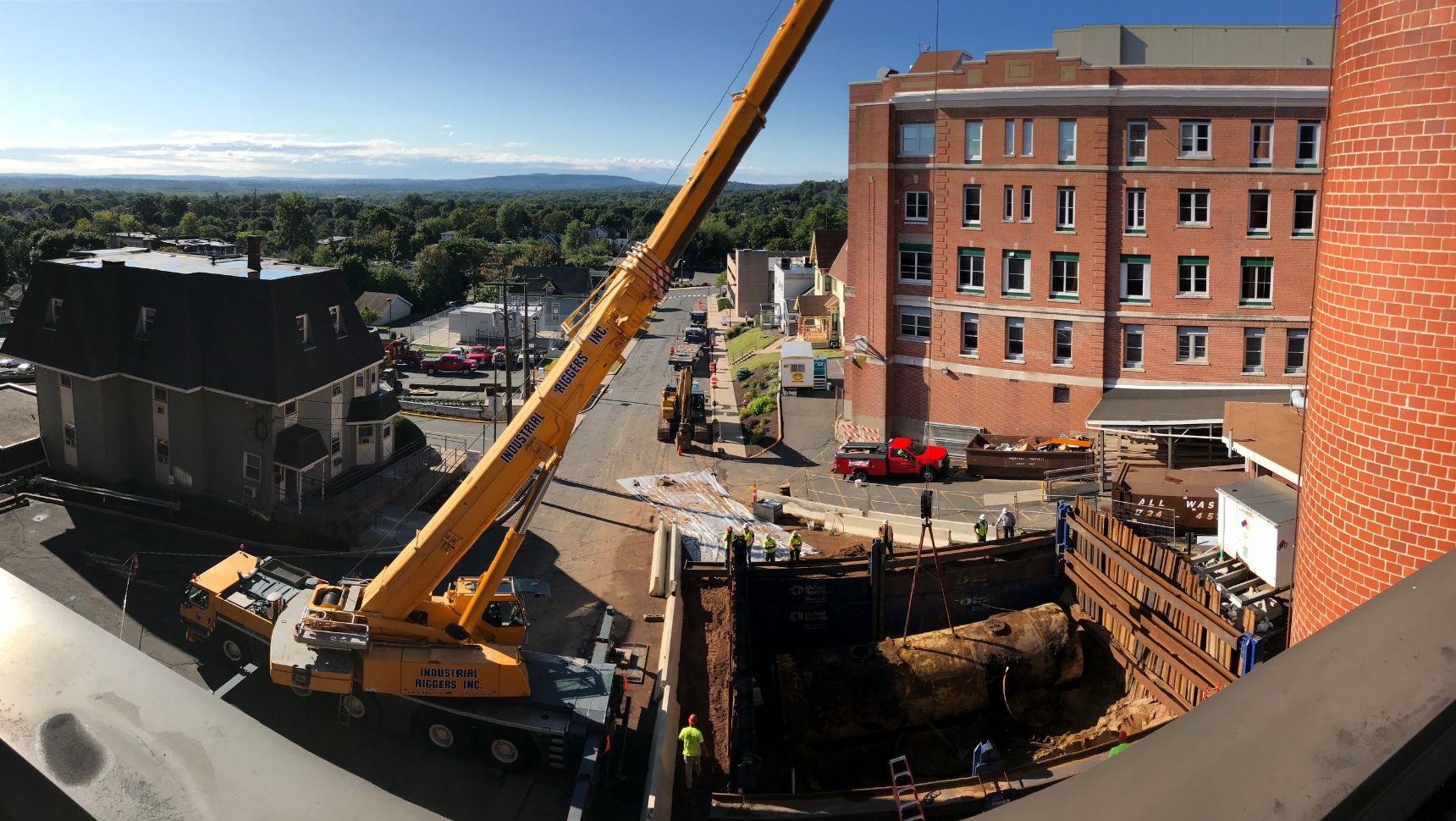
The Hospital of Central Connecticut was faced with a major challenge last year when they needed to upgrade their backup fueling system. Though their main system is natural gas, their backup heat was provided via an underground storage tank (UST) that supplied No. 6 oil. What seemed like one major challenge was actually three significant challenges wrapped up into one project. And these three challenges are being faced by many hospitals and other large facilities right now.
USTs, like almost everything else, have a useful life expectancy. Varying by state, regulations mandate how long a UST can be used before it must be replaced. In this case, the two 20,000-gallon tanks were near the end of their 30-year lives. So challenge number one was removing and replacing two rather large USTs that were located both near the maintenance and service area of the hospital and in close proximity to the hospital’s emergency entrance. The second challenge was that the original UST provided No. 6 fuel oil and the new UST would be providing No. 2 oil, which necessitated conversion of piping and burners. The third challenge was that, this being a hospital, there could not be any downtime of their backup systems and all deliveries into and out of the hospital could not be interrupted. A hospital always has to be fully operational.
This challenging, and ultimately successful, project was helped by the fact that it was a design-build project. Design-build projects are collaborative in nature. They bring together the major project leaders (the owner, the engineer, and the contractor) to identify challenges and solutions up front, to create a plan that integrates each phase and each team member’s level of responsibility, and to understand expectations. This collaboration leads to clear understanding of project scope, which leads to less change orders. Given the many steps that this project required and the need for expediency, the collaboration, single point of contact, and speed to delivery that are the hallmarks of a design-build project were integral to making this a successful project.
To overcome the major challenges of this project, the design-build team had to get creative in its approach. We knew that the first thing we had to do was make sure that the hospital had backup fuel to its burners at all times in the event that the hospital’s natural gas supply was ever interrupted during the project. Being without fully operational systems is simply not an option for a medical facility. So we brought in a temporary 4,000-gallon tank to connect to one of the facility’s three boilers. But we realized that it made sense to do the piping and burner conversion at this point in the project, not when the permanent tank was installed. The temporary tank was No. 2 fuel, as was the new permanent tank, which is a much more environmentally-friendly fuel. When the original tank was installed, No. 6 fuel was standard; it was the go-to choice last century when many facilities switched from coil to oil – it was cheap and readily available. However, the higher sulfur content of No. 6 oil increases its polluting effects, so the EPA has limited its use. The new tanks provide reliable backup heat, and they do so in a way that is less harmful to the environment.
Once we completed the conversion and installed the temporary system, ensuring that emergency fuel (heat) was readily available and that the piping and burners were ready to receive No. 2 oil, we tackled the larger challenge of replacing the old UST. The location where the UST was buried was limited in space, requiring shoring to safely excavate, and was located near both the emergency entrance and the multiple service entrances. We had to ensure that personnel, equipment, and vehicles were never blocking the emergency entrance, not even for a second. These tanks are large, and the equipment used to remove and replace them is, of course, very large as well. We had to get very creative in our limited space, while still performing tasks safely. Regarding the service entrance, the hospital provided us with a schedule of services (laundry, patient transfer, trash, food, medical supplies, air, gas, etc.) that used the loading docks. We had to ensure that there was always a route available to not interrupt the daily functions of the hospital.
I think that successfully installing two new 20,000-gallon USTs and returning the site to its pre-construction conditions would not have been possible as expeditiously had this not been a design-build project. Talking with the hospital staff made it that much easier to give them what they needed in a way that was minimally invasive. In fact, David Gunn, Hartford HealthCare’s Central Region Facilities Project Manager, noted: “As you can imagine, a tank replacement of this magnitude basically being surrounded on three sides by buildings and hospital access was a challenge! The Fuss & O’Neill team did a really nice job with coordination with the hospital and communication was on a daily basis. This was a very successful project for our facility that needed to be completed on time and on budget. Both objectives were met and we were very happy with the outcome.” Having everyone together, having a common goal, and working together to achieve a common goal instead of only planning the steps in which I was involved absolutely had a positive impact on this project. Design-build can be applied to most projects, and can save time, money, and headaches. If you’d like to learn more about the benefits, please give me a call.
Charlie Ahles, PE has more than 30 years of construction and design experience. His position provides him with both the internal technical resources of Fuss & O’Neill staff and a vast network of subcontractors, which creates design-build potential for a wide variety of projects.
We keep up-to-date on developing technologies, emerging concerns, climate projections, and new regulations. Subscribe to be the first to know how these ever-changing industry topics impact you and how we’re responding.
"*" indicates required fields